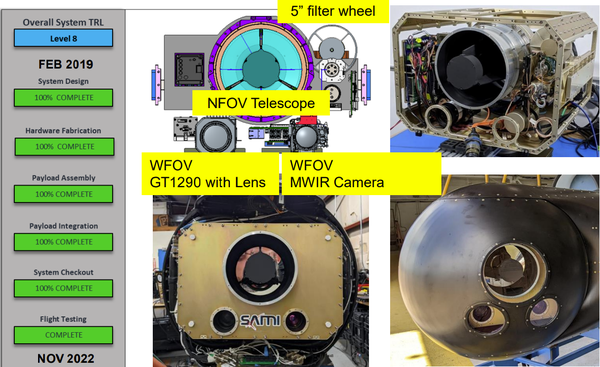
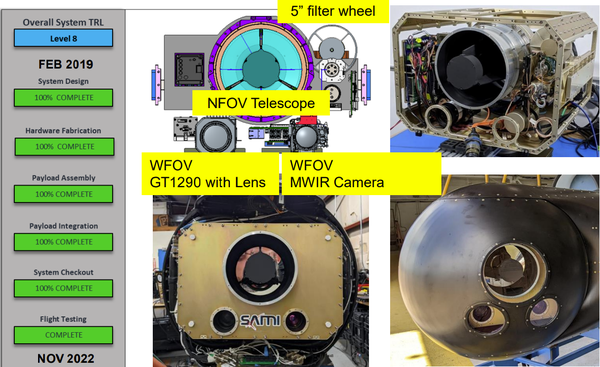
I have been working full time as a Mechanical Engineer involved in numerous projects at OKSI for the past six years. Throughout my time at OKSI, I have been responsible for the mechanical design of several products and projects for aerospace, research, and defense applications. In addition to this, I have been involved in creating rapid prototypes for R&D work by working closely with software and electrical engineers as well as manufacturers to bring my designs to life. A few projects I have been involved in are the SAMI (adjustable camera mount for HSI), the DIS (Digital Imaging System), Hydra70 seeker, autonomous ground vehicle project, remote weapon station, and much more.
In addition to my time at OKSI, I have also interned with Northrop Grumman for two summers. In the Summer of 2021, I worked closely with Mechanical Engineers in support of the communications payload for Next Generation Polar. I utilized CREO 4.0 for mechanical design of antenna suite components as well as creating drawings for components. During the Summer of 2020, I interned at Northrop Palmdale and utilized NX12 for several design projects. I worked hands on with composites and created several layups using different techniques and carbon fiber weave patterns as well as vacuum bagging layups for curing.
I contributed to the design of SAMI (SCIFLI Airborne Multispectral Imager) payload flown on a NASA WB-57 aircraft. SAMI is a multimodal imager that collects multispectral and hyperspectral data. This data will enable NASA to validate and improve modeling tools to support future missions, including landing spacecraft on Mars. SAMI was developed specifically for NASA’s Space Launch System, which emits hot plumes invisible to the naked eye. By using SAMI’s broad infrared capabilities, these plumes are rendered visible and SCIFLI will be able to collect essential data on their movement and temperature. It flew in its first active mission with Artemis I, and is planned to be used for several upcoming missions.
I designed a 6 degree of freedom, fully adjustable camera mount for one of the several imaging sensors on board SAMI. This imaging sensor mount needed an adjustment accuracy of 15 microns while being rigid enough to withstand harsh vibrations during flight. One of the biggest challenges of this project was creating a very high accuracy adjustment mechanism that is compliant while being very rigid when locked in place. I worked alongside optical, software, and electrical engineers in order to account for all aspects of the mechanical design for this mount. I made drawings for every component and worked closely with machine shops to produce the required parts. Some of these components needed a special coating because they would be directly interacting with the light path inside the HSI box. After several design iterations, a functioning mount was made and thoroughly tested before integrating with the entire SAMI payload. This camera mount proved to be successful after a data collection mission in the fall of 2023. Throughout the entire flight it maintained positional and rotational alignment.
I was responsible for the design of several actuators for the autonomous RZR project. We took a stock Polaris RZR and retrofitted cameras, sensors, computers, and actuators in order to give the vehicle full autonomy capabilities and waypoint functionality. I worked on creating actuators for both the brake and shifter on the vehicle. One of the biggest challenges with the actuator design was keeping the form factor as small as possible while having a high torque output. The areas these actuators needed to be integrated into were already very tight in terms of space. Pictures and 3D scans of the vehicle aided in the design process for these mechanisms. The first prototype actuators were mounted to the vehicle and hooked up to the ground vehicle computer for testing. Both actuators worked as intended and had almost double the torque required to actuate the shifter and brake pedal. To provide positional feedback both actuators incorporated absolute encoders which made it a fully closed loop system. I had the opportunity to do very extensive testing in different environments , and was given creative freedom to come up with my own design for the two actuators. After drafting up designs for these actuators I worked with several mechanical engineers to review these designs in order to make improvements or implement other specific design aspects. We successfully demonstrated autonomous waypoint mission capabilities at the 2022 tough stump event. We were able to drop waypoints on a map and the vehicle accurately navigated to each with great accuracy.
I was a part of our GPS-Denied development effort supporting flight operations and mechanical design for the vehicle. I was responsible for building a small VTOL UAV capable of carrying a processor, cameras, and other sensors used for GPS denied software algorithms. I worked with software engineers to select components and designed fixtures and mounts for these components. We took a COTs UAV package and completely overhauled it with our own electronics and sensors to serve as a testbed for algorithm development. On this project I spent most of my time building two UAVs which included assembling the airframe, soldering all the electrical components such as motors, actuators, sensors, cameras, and on board flight computers. In addition to building several UAV's I was also the sole UAV pilot on this program. I spent a lot of time testing and tuning the entire system to make flight more stable. This involved tweaking parameters, tuning PID loops and IMU filtering and a lot of flight testing. This UAV can take off vertically and then transition into horizontal flight. The most challenging part of this project was getting the UAV to have a stable transition. Overall this project proved to be a success, we were able to transition into horizontal flight and successfully preformed GPS-denied waypoint navigation.
One of the most challenging and coolest projects I've been a part of is this Hydra-70 seeker design, manufacturing, and integration effort. I led the mechanical design and production effort for this project. The goal for this project was to recover imaging and sensor data from a firing event at a soft catch target. One of the requirements was to be able to physically recover all the data which was stored on an onboard black box data logger. This proved to be very challenging because this rocket is airborne for less than 10 seconds and reaches a max speed of over 1.5 mach. The forces seen at impact are high and designing a data storage solution to survive these forces required thorough testing and multiple iterations. The seeker includes mounting provisions for an onboard computer, imager, sensors, as well as its own power source. I worked closely alongside mechanical and electrical engineers, and was in close contact with engineers from BAE to coordinate specific design aspects and integration onto their APKWS system. After the design phase, I worked closely with several machine shops to produce all the required parts and coordinated assembly efforts. Our first ever launch event was a success, we were able to capture data and successfully recover the seeker and stored data.
Drones